Lean Green Construction Machines
Ireland is on its way to becoming a centre of excellence for Lean Construction, a discipline that sees all participants working on a cycle of continuous improvement to increase value and reduce waste.
There is a wind of change blowing through the construction industry in Ireland – it is not just that there is a sense that there are better times ahead, economically, there is also a growing sense that we are embarking upon a better way of doing things. This new approach to building is being called ‘Lean Construction’, though some say it isn’t a new approach at all, some say it is the old-fashioned values of trade and craft coming to the fore.
Lean Construction is a way to set up and design a construction project to minimise waste of materials, time and effort in order to generate the maximum possible amount of value for all parties – the owner, the designer, the contractor and sub-contractors.
The lean philosophy first became current in Western manufacturing at the start of the millennium when American and European businesses tried to emulate the success achieved by Toyota in building a worldwide reputation for outstanding quality. Many lean concepts and lean management tools are based on work practices developed by the Japanese car manufacturer, such as Just-in-Time supply chain management, but there are many who say that Henry Ford was a lean champion, ahead of his time, because of the way he standardised the production process and worked to eliminate waste.
The elimination of waste is key to lean thinking, Lean Manufacture and Lean Construction. Commonly, there are seven types of waste that can be identified in any process, be it on a factory floor or a building site. These seven wastes are remembered using the acronym ‘TIMWOOD’, which stands for and Transport, Inventory, Motion, Waiting, Over-processing, Overproduction and Defects. If you can eliminate or reduce any of these wastes, for example in Transport the number of times raw materials have to be moved from one location to another on site, then you automatically increase productivity, reduce costs and/or increase profitability.
Since 2009, Enterprise Ireland has been offering training and consultancy supports to help companies adopt lean business practices and since 2013 the Construction Industry Federation has been offering its members a Lean Healthcheck to help identify the seven streams of waste and to plan to develop focussed company-toolkits to address those wastes and help companies stay competitive.
So far, some 700 companies have taken part in Enterprise Ireland’s Lean Start programmes and that figure is expected to rise to 3,500 over the next five years. Over a year ago, Forfás examined the performance of 344 Enterprise Ireland client companies that had reached an advanced stage of progress in implementing lean initiatives. The study found that companies using lean concepts and tools were 20% more productive than companies without lean and that employment in lean firms was 11% higher; there were some 6,000 additional people in employment because of the profitability of the 344 firms in the study.
In the construction sector, it can be argued that Ireland is lagging behind the UK in adopting lean techniques. The Construction Lean Improvement Programme (CLIP) has been running in Britain since 2003 and is aimed at improving the financial performance of construction industry firms, while also ensuring they provide a better product and service to customers. That said, the Irish building industry is fast catching up with its counterparts across the Irish Sea, thanks chiefly to the efforts of the Lean Construction Institute Ireland’s initiatives.
LCII
Founded in the US in 1997, the Lean Construction Institute (LCI) aims to reform the management of production in design, engineering and construction for capital facilities. LCI founders Glenn Ballard and Greg Howell describe Lean Construction as “a new and transformational way to design and build capital facilities”.
According to Howell and Ballard, ‘Lean Construction is a production management-based project delivery system emphasizing the reliable and speedy delivery of value. It challenges the generally-accepted belief that there are always trade-offs between time, cost and quality’.
The first Lean Construction Institute (LCI) Community of Practice (CoP) in Ireland was launched last April at an event designed to raise awareness of Lean Principles in the Irish Architectural, Engineering and Construction (AEC) sector and to demonstrate how the members can implement lean as a collective group through knowledge sharing, innovation through research, and deep collaboration between the four main sectors – owners, designers, contractors and trades people.
Notably, the event attracted 200 delegates – when similar events were held in the US and the UK, the number of participants turning up was less than 50. One reason for the higher level of participation in Ireland is that the Community of Practice here is currently offering free-of-charge participation, so that even the smallest contracting or sub-contracting firm can become involved. So far this free-of-charge model has been made possible by sponsorship – Intel sponsored the inaugural LCI COP event last year and since then events have been sponsored by Jones Engineering, Mercury Engineering, CIF and M+W Group with PM Group sponsoring the next event on March 25th.
One of Ireland’s leading experts in lean business, Dr Richard Keegan of Enterprise Ireland says that overseas people are taking a very keen interest in what is happening in Ireland, because of the way lean is taking too here so quickly. “The construction sector is at a very early stage of adoption of lean principles, but already people overseas are taking an interest in what is happening here because we seem to be gaining traction more quickly than elsewhere,” said Keegan. “I think it is because the people who are leading this movement are so keen to share what they have learned. The growth is 100% organic. The first companies to try lean were the larger companies, but these big guys are now saying ‘we have tried this, it works and we are delighted to share it with others. It is a classic Irish approach. There is something about Ireland where we like one another and want to help one another.
“Lean isn’t primarily about using particular business tools that is not what is the most important. It is a mindset, it’s about engaging with people so that they do a better job and are more satisfied with the job they do. Lean is based on respect for people, the people at the coalface, that is fundamental. It is about allowing themselves to be more creative, to challenge themselves to things better than they did previously.
“I was talking to a site supervisor and he said there was nothing new in this, it was really about good leadership, coaching your workers to get the best out of them and there is a truth in that.
“Toyota, who have been championing lean for 80 years, are seen as the car manufacturer whose cars have the highest resale value. But the same is true in construction, there are some builders whose second hand homes command a higher price because they are better built. If you have a commitment to quality, you gain a reputation for quality.
“There are a whole load of macro-benefits to Lean Construction. Overall, it should mean that we all get a better built environment, a better place to live and that has the potential to allow us to differentiate ourselves from other countries when seeking foreign direct investment or FDI. Having a good built environment shows the world that we are highly-educated people who can build and run sophisticated manufacturing plants and research centres. It also means that we put ourselves in a position where we can export our skills and win construction contracts overseas.”
One of the COP founders, Paul Ebbs is researching how best to embed lean in the Irish AEC sector as part of a PhD. He says that lean is taking root in Irish construction thanks to the dedicated voluntary efforts of people in the industry who have already seen that lean succeeds. “Lean is a new way of looking at things,” he says. “Once you have worked with Lean Construction and seen it work, you usually don’t want to go back to old ways of working.
“Within LCI Ireland, ten tactics have been identified to help embed lean in the AEC sector. These are – developing and scripting a clear LCI Ireland message; developing a dedicated LCI Ireland Website; develop an LCI Ireland starter-pack for interested companies; developing a training pack for lean champions within companies; developing a library of case studies, industry benchmarks and references; setting up an owner’s forum; encouraging industry personnel and academics to submit papers to the International Group for Lean Construction Conference; promoting lean through site tours and practical demonstrations; developing a finance plan to make LCI Ireland self-sustainable and to promote lean through LCI Ireland Awards.”
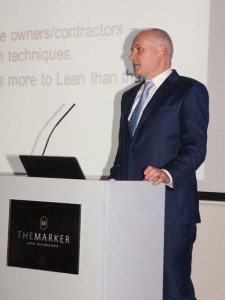
The economic case
More importantly for the bottom line, there are micro reasons for taking the principles of Lean Construction on board says Fearghal Scanlon of M+W Group, a core member of the LCII Community of Practice. He said: “Lean saves us money, it saves money for the client, it makes us more efficient and a better company and a happier place to work.”
That last trait of lean businesses – that employee job satisfaction is high – is also a trait that has an impact on the bottom line. Higher levels of job satisfaction mean fewer absentees and less churn in staff, which in turn means fewer unexpected delays because of manpower problems and, because you are not having to recruit replacement staff, lower induction and training costs.
Scanlon says that lean is chiefly a state of mind, where everyone involved works to eliminate waste and to make construction more efficient. As an example, he says that companies using Lean Construction pay more attention to how they set up a site. “For example, look at office layouts,” he says. “Traditionally, the designer, the contractor and the owner would have three separate offices on a site, and they might only meet together once a week for an hour and would communicate in the meantime via email. On our projects now we like to see the designer, the contractor and the owner representatives sitting side by side, sharing office space, which is something that breaks down barriers and gets people working together. Instead of sending each other emails describing a problem, the reps go down to the location and look at the problem together.
“Similarly, how you plan your site layout can make a huge difference. For example, where do you put the canteen? On a very large with 1,000 workers on it, if it takes them 10 minutes to get to the canteen and 10 minutes to get back to their place of work and they go to breakfast and lunch, that is 40 minutes each or 800 man hours a week. Relocating the canteen, or maybe even having two canteens, might have a higher upfront cost but the saving in wasted man hours and the improvement in employee job satisfaction can be huge!
“Lean is not just for the big guys like – BAM, Jones Engineering, Mercury and the M+W Group, it’s for the guys who are building the house extension – a simple lean tool would be a whiteboard on site where all snags are recorded as they come to the attention of the contractors workers, the subbies, the architect and the designer and then as each snag gets tackled a line is put through it. At the end of each week, everyone can see how many snags have been identified, how many have been tackled and how many are still on the list.”
“Lean is just another name for continuously improving how we deliver projects by doing things better, faster or cheaper and focusing on what the client values” said Gary Widger, head of innovation and change at Mercury Engineering.
“In a way we have always been doing it, as Mercury’s culture has always driven the pursuit of excellence. What has changed is that the term ‘Lean’ has emerged as the global language for Productivity. It’s part driven from the recession but is more so a follow on from the great progress on Safety then Quality in our industry in the 90’s and 00’s. Lean has now developed a critical mass in construction through design, offsite and installation.
“Leading clients want to work with Lean partners as it leads to more successful outcomes for all companies. The industry now recognizes that Lean benefits everyone working on a project, the contractor, subcontractors, the designer and the owner themselves.”
“Leveraging BIM, we now manufacture and modularise a significant scope of work off-site in Newbridge. This is giving us improvements in safety, in quality and our ability to deliver to schedule. For example, when working on the Kerry Group Innovation Centre, we used off site modularization successfully to manufacture a 40-metre long riser that was then moved onto site and placed in position in one morning. In Sweden, we are working on a data centre, where off-site construction is allowing us to provide schedule certainty while it is -20°C outside. By working off site we have are extending the construction season without bringing expensive heating and lighting costs to the construction site itself. That is a practical application of Lean Construction.”
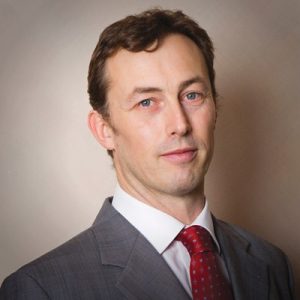
“Productivity onsite installation is still crucial. To drive improvements on project sites we have implemented a right first time indicator, this feeds into our use of the core lean principle, DMAIC, define, measure, analyse, improve and control. We define our goal, measure our results using the indicator, analyse our data and make improvements utilizing accurate data. Since the implementation of the indicator our right first time spool installation has risen to more than 98%, also on our largest mechanical project line test fails have reduced to zero percent. This is Lean in its purest form.
“If there is a construction company owner or manager reading this and is interested in adopting lean, I would say that the CIF’s Lean Healthcheck programme is a great place for them to start. Working openly with you peers helps fast track the adoption of Lean in companies. Collaboration is crucial it ensures we all benefit from the Lean rising tide.
Jones Engineering – Lean Culture
At Jones Engineering the company has worked hard to develop a lean culture among all levels of staff, says electrical division manager Kevin White. He says: “Jones has been working specifically around Lean since 2004, when we did the CLIP programme in the UK, because we were doing earned value analysis (EVA) on our projects and we saw that there was a lot of waste in our systems that we should deal with. From this introduction, we saw there was a lot we could do ourselves towards continuous improvement year-on-year, with this being led initially by our productivity manager operating through our supervisors.
“In 2006 and 2009, we did an online poll of all our managers – from the contract managers right down to the charges on the floor – and following this survey we started to concentrate on those areas with the highest amount of waste, as identified by the people who work for us. Then we started to have an over-all look at our processes and that started us wanting to get our contractors and our customers involved. In the last two or three years, clients are willing to get involved – they have heard about lean and they want to learn more. With our sub-contractors, they had to work lean because of the way their contracts with us were organised, but having seen the benefits of working lean they have gone on to start to look at their own processes and how they can be improved.
“We have achieved substantial increases in productivity – in our containments area, for example, we have increased productivity by 40 to 50% following a series of incremental improvements.
We used to order containments in 3m lengths and then cut them by hand using hack saws and put holes in them using drills, then we moved from that to using band saws and punches for holes and now we are getting the containments manufactured to size, pre-cut and pre-punched, and delivered ready-to-fit. This is made possible because we use BIM to produce isometric drawings for the containments supplier.
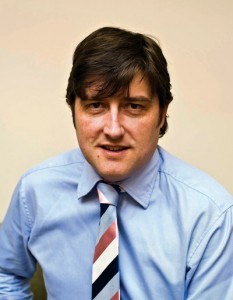
“When we started on lean, we adopted a bottom up approach, so that we could create a common language about continuous improvement in-house. Now we are able to push from top-down, because there is an understanding throughout the company of what Lean Construction is. Since 2004, any new supervisor goes through Lean Construction training and the company, which employs in the region of 3,000 people, has four dedicated lean training people. If someone comes up with a lean initiative or an idea to improve productivity, not only do we see that the idea is adopted we publish it in our own in-house Lean Times news letter to promote the good practice across the company.
“My own background is that I am a time served electrician and I have a lot of respect for the traditions of the craft – but there are new technologies emerging all the time that can be leveraged to improve productivity. There is always some waste that can be eliminated; there are always further improvements that can be achieved.”