Autodesk helps BMCE stand tall with record-breaking build
The company behind the two tallest modular buildings in the world, Barrett Mahony Consulting Engineers (BMCE) is a dedicated user of Autodesk Building Design Suite 2015.
Founded in 1994, BMCE is a co-developer of a volumetric modular building solution, where the structure of the building is included in the elements fabricated off site. It was first used to create 366 apartments, in six blocks, at Stepaside in Dublin.
Notably, the Vision Modular System was used on the tallest modular building in the world, student accommodation in Wolverhampton, built using 805 modules and consisting of three blocks, the highest being 25 storeys tall. The BMCE solution is also used on the world’s second tallest modular building, the Novotel hotel and a mixed residential development near Wembley Stadium in London which has a 20-storey modular-built residential tower.
Modular building techniques are usually only seen on buildings up to 10 storeys in height, so the Wolverhampton and Wembley developments have generated worldwide interest, says BMCE director Michael Hough.
BMCE has a full-time staff of 50, including five partners, and has offices in Dublin and London. In addition to modular building, the practice has significant experience in residential, commercial, refurbishment, facade retention, and specialist masonry and precast solutions.
Hough says building information modelling (BIM) is now used on 60-70% of Barrett Mahony projects, and is being integrated into modular building projects.
“Modular building work involves early decisions on everything in the building from structural members to pipes, switches, tiling, and paint colours,” said Hough. “With early decisions needed and also many of these elements completed offsite the coordination of all parts of the build need to respect the other disciplines and their requirements. We work very closely with the modular manufacturer and the overall design team to achieve a coordinated construction project.”
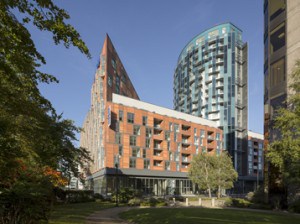
As a company, BMCE places a strong emphasis on technical excellence and cost effective design and it has continuously invested in state-of-the-art computer technology in order to provide competitive and up-to-date services to its clients. Hough said: “With the industry moving in the direction of BIM we are committed to keeping as close to the leading edge as our projects will allow. Initially it was difficult to see the benefits as there was a significant learning and customisation curve to achieve a similar standard of output to the previous drawings. We floated the licences around the office allowing anyone interested to use the software and actively encouraged use of the home licences. Staff that used the software on a regular basis quickly reached high levels of productivity. Collaboration across disciplines is important, but in-house it is invaluable.”
“Licence costs are comparative to AutoCAD licences. As part of our BIM training, we have trained in house using more experienced staff as mentors for the less experienced as part our CPD and Quality Assurance policies. There is also an initial time cost, related to the learning curve and customisation of output to match existing 2D drawing standards.
“The architects we work with on these projects are also using BIM and seeing the benefits. Once all team members, or even a majority of team members, are operating on a 3D model the effectiveness is very significant. In the medium to long term, the software will definitely be a saving and help very significantly with coordination.
“We are in the process of linking software from the model through to analysis, and into further software that will allow direct linking to CNC machines. This involves considerable effort and customisation but the benefits are significant to a system build.
“With current architectural trends, we are working more and more often on projects with complex geometry. BIM may have partly been a catalyst for this, but the fact we can collaborate easily with architects and designers makes it substantially easier to co-ordinate and complete these projects.”
Indeed, BIM saves time and money, says Hough. “Many issues with design or construction can be ironed out and solved prior to the commencement of construction.”
Indeed, long before construction on a project commences, BIM helps Barrett Mahony win business, as the 3D modelling helps clients to fully understand the scope of their initial concept designs. Hough says: “BIM gives us a competitive advantage. At tender stage and early design stage, with 3D renders and animations, you can give your clients a feel for their completed project with the added advantage of ‘the Wow factor’!” Diatec, an Autodesk Gold Partner, is the chosen supplier to Barrett Mahony, for all their Autodesk design software and solution specific hardware requirements.